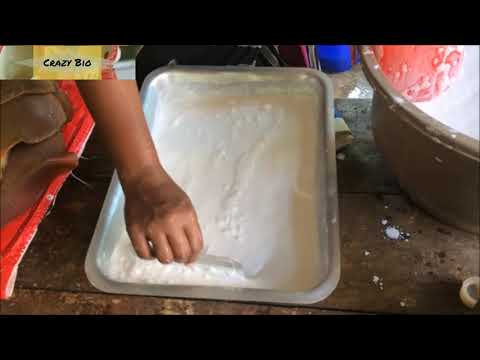
المحتوى
في أواخر ثلاثينيات القرن الماضي ، استخدمت الولايات المتحدة أكثر من نصف إمدادات المطاط الطبيعي في العالم. اليوم ، يمكن العثور على المطاط الطبيعي في أكثر من 50000 منتج مصنّع في الولايات المتحدة ، وتستورد الولايات المتحدة أكثر من 3 مليارات رطل من المطاط الطبيعي كل عام. أكثر من 70 في المئة من المطاط المستخدمة في عمليات التصنيع الحديثة ، ومع ذلك ، هو المطاط الصناعي.
خلفية المطاط الطبيعي
المطاط الطبيعي يبدأ اللاتكس. يتكون اللاتكس من البوليمر المسمى polyisoprene المعلق في الماء. تتكون جزيئات السلسلة الطويلة من العديد من الوحدات (بولي) الفردية (mers) المتصلة ببعضها من البوليمرات. المطاط هو شكل خاص من البوليمرات يسمى المطاط الصناعي ، وهذا يعني أن جزيئات البوليمر تمتد ومرنة.
ينتج أكثر من 2500 مصنع مادة اللاتكس ، وهي مادة تشبه اللبن. قد تكون الحشائش أكثر مصانع إنتاج اللاتكس شيوعًا للعديد من الناس ، ولكن اللاتكس التجاري يأتي من شجرة استوائية واحدة ، Hevea brasiliensis. كما يوحي الاسم ، نشأت شجرة المطاط في أمريكا الجنوبية الاستوائية. منذ أكثر من 3،000 عام ، حضرت حضارات أمريكا الوسطى اللاتكس مع عصير المجد الصباح لإنتاج المطاط. تغيير نسبة اللاتكس لعصير المجد الصباح غيّر خصائص المطاط. من الكرات المرتدة إلى الصنادل المطاطية ، عرف سكان أمريكا الوسطى المطاط واستخدموه.
قبل عام 1900 ، جاء معظم المطاط الطبيعي من الأشجار البرية في البرازيل. مع بداية القرن العشرين ، فاق العرض والطلب الإنتاج مع تزايد شعبية الدراجات والسيارات. أدت البذور المهربة من البرازيل إلى مزارع الأشجار المطاطية في جنوب شرق آسيا. وبحلول الثلاثينيات ، تراوحت استخدامات المطاط الطبيعي من الإطارات على السيارات والطائرات إلى 32 رطلاً التي عثر عليها في أحذية الجنود والملابس والمعدات. بحلول ذلك الوقت ، كانت معظم إمدادات المطاط الأمريكية تأتي من جنوب شرق آسيا ، لكن الحرب العالمية الثانية عزلت الولايات المتحدة عن غالبية إمداداتها.
عملية تصنيع المطاط الطبيعي
تبدأ عملية تصنيع المطاط الطبيعي بحصد مادة اللاتكس من أشجار المطاط. يبدأ حصاد اللاتكس من أشجار المطاط بتسجيله أو تقطيعه إلى لحاء الشجرة. يتدفق اللاتكس إلى فنجان متصل بأسفل الشجرة. تتراكم مادة اللاتكس من العديد من الأشجار في خزانات كبيرة.
الطريقة الأكثر شيوعًا لاستخراج المطاط من اللاتكس تستخدم التخثر ، وهي عملية تخثر أو تسمم مادة البولي إيزوبرين في كتلة. يتم تحقيق هذه العملية بإضافة حمض مثل حمض الفورميك إلى اللاتكس. تستغرق عملية التخثر حوالي 12 ساعة.
يتم ضغط الماء من تجلط المطاط باستخدام سلسلة من البكرات. يتم تجفيف الألواح الرقيقة الناتجة ، التي يبلغ سمكها حوالي 1/8 بوصة ، فوق رفوف خشبية في بيوت الدخان. تتطلب عملية التجفيف عمومًا عدة أيام. يتم طي المطاط البني الداكن الناتج ، والذي يُطلق عليه الآن صفائح الدخان المضلعة ، في بالات لشحنه إلى المعالج.
ليس كل المطاط يدخن ، ولكن. يسمى المطاط المجفف باستخدام الهواء الساخن بدلا من التدخين ورقة الهواء المجفف. هذه العملية تؤدي إلى درجة أفضل من المطاط. يتطلب المطاط عالي الجودة الذي يطلق عليه مطاط الكريب الشاحب خطوتين للتخثر يتبعهما تجفيف الهواء.
صنع المطاط الصناعي
تم تطوير عدة أنواع مختلفة من المطاط الصناعي على مر السنين. كل ذلك ناتج عن بلمرة (ربط) الجزيئات. عملية تسمى سلاسل بلمرة الإضافة تجمع الجزيئات في سلاسل طويلة. هناك عملية أخرى ، تسمى بلمرة التكثيف ، تعمل على التخلص من جزء من الجزيء حيث ترتبط الجزيئات ببعضها. تشتمل أمثلة البوليمرات الإضافية على المطاط الصناعي المصنوع من polychloroprene (مطاط النيوبرين) ، والمطاط المقاوم للزيت والبنزين ، والمطاط الستايرين بوتادين (SBR) ، المستخدم للمطاط غير المرتد في الإطارات.
بدأ البحث الجاد عن المطاط الصناعي في ألمانيا خلال الحرب العالمية الأولى. ومنع الحصار البريطاني ألمانيا من تلقي المطاط الطبيعي. طور الكيميائيون الألمان بوليمر من وحدات 3 ميثيل أيسوبرين (2،3-ثنائي ميثيل -1،3 بوتادين) ، من الأسيتون. على الرغم من أن هذا البديل ، وهو مطاط الميثيل ، كان أدنى من المطاط الطبيعي ، فقد صنعت ألمانيا 15 طنًا شهريًا بنهاية الحرب العالمية الأولى.
أدت البحوث المستمرة إلى المطاط الصناعي أفضل جودة. النوع الأكثر شيوعًا من المطاط الصناعي المستخدم حاليًا ، Buna S (ستيرين بوتادين المطاط أو SBR) ، تم تطويره في عام 1929 من قبل الشركة الألمانية I.G. فاربن. في عام 1955 ، طور الكيميائي الأمريكي صموئيل إميت هورن جونيور بوليمر يحتوي على 98 في المائة من مادة البولي إيزوبرين بنسبة 1.4 في المائة يتصرف مثل المطاط الطبيعي. تم استخدام هذه المادة مع SBR للإطارات منذ عام 1961.
تجهيز المطاط
يصل المطاط ، سواء كان طبيعيًا أو صناعيًا ، إلى مصانع المعالج (المُصنع) على شكل بالات كبيرة. بمجرد وصول المطاط إلى المصنع ، تمر المعالجة بأربع خطوات: التركيب والخلط والتشكيل والفلكنة. تعتمد تركيبة وطريقة تركيب المطاط على النتيجة المقصودة لعملية تصنيع المطاط.
يضاعف
يضيف التركيب مواد كيميائية ومواد مضافة أخرى لتخصيص المطاط للاستخدام المقصود. يتغير المطاط الطبيعي مع درجة الحرارة ، ويصبح هشًا مع البرد وفوضى لزجة مع الحرارة. تتفاعل المواد الكيميائية المضافة أثناء التركيب مع المطاط أثناء عملية الفلكنة لتثبيت البوليمرات المطاطية. قد تشمل الإضافات الإضافية مواد حشو معززة لتعزيز خصائص الحشوات المطاطية أو غير المعززة لتمديد المطاط ، مما يقلل التكلفة. يعتمد نوع الحشو المستخدم على المنتج النهائي.
أكثر حشو التسليح استخدامًا هو الكربون الأسود ، المستمد من السخام. الكربون الأسود يزيد من مقاومة الشد للمطاط ومقاومة التآكل والتمزق. الكربون الأسود يحسن أيضا مقاومة المطاط للتدهور فوق البنفسجي. معظم منتجات المطاط سوداء بسبب حشو أسود الكربون.
بناءً على الاستخدام المخطط للمطاط ، يمكن أن تشمل المواد المضافة الأخرى المستخدمة سيليكات الألومنيوم اللامائية مثل مواد حشو معززة ، بوليمرات أخرى ، مطاط معاد تدويره (عادةً أقل من 10 بالمائة) ، مركبات تخفف من التعب ، مضادات الأكسدة ، مواد كيميائية مقاومة للأوزون ، أصباغ تلوين ، مواد بلاستيكية ، تليين الزيوت ومركبات إطلاق العفن.
خلط
يجب أن يتم خلط المواد المضافة بالكامل في المطاط. تجعل اللزوجة العالية (مقاومة التدفق) من المطاط عملية الخلط صعبة دون رفع درجة حرارة المطاط عالية بما يكفي (تصل إلى 300 درجة فهرنهايت) للتسبب في عملية الفلكنة. لمنع الفلكنة المبكرة ، يحدث الخلط عادة على مرحلتين. خلال المرحلة الأولى ، يتم خلط المواد المضافة مثل أسود الكربون في المطاط. يشار إلى هذا الخليط باسم ماستر. بمجرد أن يبرد المطاط ، تضاف المواد الكيميائية الخاصة بالكبريت وتخلط في المطاط.
تشكيل
يحدث تشكيل منتجات المطاط باستخدام أربع تقنيات عامة: البثق ، والتقويم ، والطلاء ، أو الصب ، والصب. يمكن استخدام أكثر من تقنية تشكيل ، اعتمادًا على المنتج النهائي.
يتكون البثق من إجبار المطاط عالي البلاستيك من خلال سلسلة من البثق اللولبي. يمر التقويم في المطاط عبر سلسلة من الفجوات الأصغر حجمًا بين الأسطوانات. تجمع عملية البكرة بين القذف والتقويم ، مما ينتج عنه منتج أفضل من أي عملية فردية.
يستخدم طلاء عملية التقويم لتطبيق طبقة من المطاط أو لفرض المطاط في النسيج أو مواد أخرى. يتم تصنيع الإطارات وخيام القماش المضادة للماء ومعاطف المطر وأحزمة النقل وكذلك أطواف قابلة للنفخ من مواد الطلاء بالمطاط.
منتجات المطاط مثل باطن الأحذية والكعب ، والحشيات ، والأختام ، وأكواب الشفط وتوقف الزجاجة يتم إلقاؤها باستخدام قوالب. صب هو أيضا خطوة في صنع الإطارات. الطرق الثلاثة الأساسية لتشكيل المطاط هي قولبة الانضغاط (المستخدمة في صناعة الإطارات من بين المنتجات الأخرى) ، قولبة النقل وصب الحقن. يحدث تقسية المطاط خلال عملية التشكيل بدلاً من كونه خطوة منفصلة.
تقسية المطاط بالكبريت
الكبريت يكمل عملية إنتاج المطاط. ينتج عن الكبريت روابط متقاطعة بين بوليمرات المطاط ، وتختلف العملية حسب متطلبات منتج المطاط النهائي. يؤدي الارتباط المتبادل الأقل بين البوليمرات المطاطية إلى إنشاء ليونة أكثر مرونة من المطاط. تؤدي زيادة عدد الوصلات المتقاطعة إلى تقليل مرونة المطاط ، مما يؤدي إلى زيادة صعوبة المطاط. بدون الفلكنة ، يظل المطاط لزجًا عندما يكون حارًا وهشًا عندما يكون باردًا ، وسيتعفن بسرعة أكبر بكثير.
يتطلب الفلكنة ، الذي اكتشفه تشارلز جوديير في عام 1839 ، إضافة الكبريت إلى المطاط وتسخين الخليط إلى 280 فهرنهايت لنحو خمس ساعات. يستخدم الفلكنة الحديثة بشكل عام كميات أصغر من الكبريت مع مواد كيميائية أخرى لتقليل وقت التسخين إلى 15 إلى 20 دقيقة. تم تطوير تقنيات الفلكنة البديلة التي لا تستخدم الكبريت.